For the past 40 years, when the oil and gas industry thought of bolt lubricant, it focused on disassembly — i.e. the breakout torque seen at the bolt head or at the nut of the fastener.
What went unexplored until recently was how lubricant affects the Nut Factor on a fastener, which then affects tightening torque, and therefore effects the bolt tension.
But that’s just the beginning.
Through years of research and first-hand experience, we have found that many lube manufacturers don’t know how their lube performs in the field. They often don’t understand the difference between friction coefficient and Nut Factor.
That’s a problem, because you reach the applied torque on your fastener through understanding your Nut Factor. If those numbers are off, then your final torque values will be incorrect no matter what your torque reading might be.
In this article, we’ll help you avoid those problems by explaining:
- What is Bolt Lubricant?
- A Brief History of Bolt Lubricant
- Why You Use Bolt Lubricant
- How Much Bolt Lubricant to Use
- How to Apply Bolt Lubricant
- Bolt Lubricant Torque Chart
What is Bolt Lubricant?
Any lubricant is designed to reduce friction and wear between two surfaces in contact. Bolt lubricant is a little more complicated than that.
In the past, bolt lubricant has been associated with disassembly, and therefore many in the oil and gas will refer to it as “anti-seize.” But bolt lubrication is also crucially important for assembling flanges properly.
Using proper bolt lubrication practices will allow assemblers to achieve the ideal torque with a low degree of bolt scatter (which we define as differences among torque levels on different bolts holding together the same flange).
Proper bolt lubrication means:
- Consistent frictional properties: In order to determine your torque value, you have to understand, and solve for your K-factor. K-factor, which can also be called “nut factor,” is an experimental number. It is not adequate to use a friction coefficient or a friction factor calculation. In fact, PCC-1 just took out Appendix J which is the Friction Factor Calculation.
- Adequately Lubricated Fasteners: There are very few situations in bolting together flange joints where you can over-lubricate a stud. You should always be able to see a bead of lube “squish” out the bottom of the nut. This means that you have put adequate lubricant on all surfaces that need it.
- Lower Breakout Torques (no galling): Galling is a form of wear caused by adhesion between sliding surfaces. When a material galls, some of it is pulled with the contacting surface, especially if there’s large amount of force compressing on the surfaces together. Certain lubricants, such as nickel lubricants, can actually cause galling.
- Physical and chemical stability: In the past, the petrochemical industry used copper-based lubes in the past as their standard. However, they discovered these types of lubes don’t play well with hydrogen and can lead to hydrogen embrittlement, which can corrode, crack, or otherwise deteriorate surfaces. Then the industry moved to nickel-based lube, but there was another problem: It causes galling to accelerate. Now the industry has moved to moly lube. Moly lube is technically a mineral, helps prevent galling, and is good for most environments.
- Ease of application: The ability to apply lubrication is a different subject than adequate lubrication. Why? If the lube can’t come out of the can because it’s a solid at lower temperatures, an assembler won’t be able to apply it adequately.
A Brief History of Thread Lubricant
As we mentioned earlier, bolt lubricants were initially thought of as anti-seize. Companies like Jet-Lube have produced anti-seize thread lubricants for 70+ years for the upstream industry. To this day, the use of copper-based lubricant Kopr-Kote(TM) is the standard lubrication in the field.
Therefore it doesn’t seem unreasonable that when the rest of the petrochemical and power industry started to focus on anti-seize products for a bolted joint, they turned to those copper-based lubricants. But they discovered copper lube was not good for all systems because it doesn’t play well with hydrogen.
Instead, the industry then turned to nickel-based lubricants. This type of lube was considered good because of its high-temperature rating, up to 2500 degrees Fahrenheit. (But note: That is the melting point of nickel and not a good method for determining what a good lube looks like.)
Recently the petrochemical industry has moved to molybdenum disulfide, which is also called “moly” lube. Currently this is the best type of lube for assembling bolted joints, because it does not cause hydrogen embrittlement if mixed with the correct chemicals.
(Note: Pure moly lubricants are not recommended around hydrogen. Check with the manufacturer.)
Why Use Bolt Lubricant?
There are two main reasons why lubricated fasteners are better than non-lubricated fasteners.
1. Galling
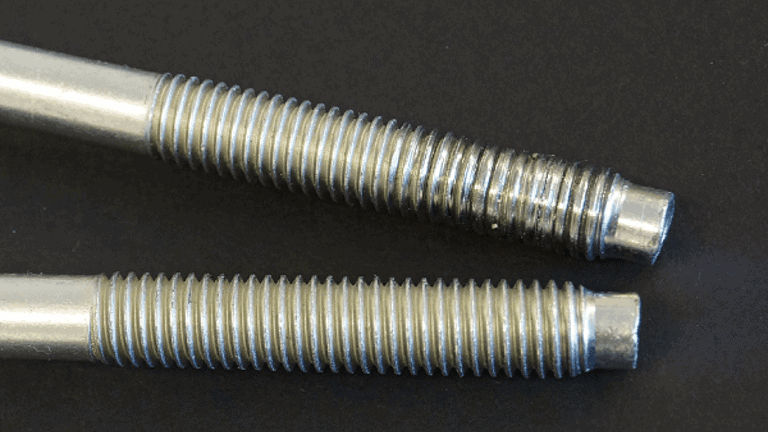
Galling is one of the most frustrating things we run into in the field as assemblers.
The true definition of galling comes from ASTM G40, and it says galling is form of surface damage arising between sliding solids distinguished by microscopic, usually localized roughening and creation of protrusions, i.e. lumps, above the original surface.
So what does that mean to the assembler?
It means we’re grinding steel on steel to stretch steel. That’s what we’re doing when we use torque. So if we want to get rid of galling, one of the best ways to is to properly lubricate.
The other part of preventing galling is in what type of lubricant you are using. That’s why you’ve seen an increase of molybdenum disulfide lubricants (a.k.a “moly” lubricants) in the industry.
2. Achieving Proper Bolt Torque: An Introduction to K-Factor
Here we need to discuss:
- Non-Lubricated Bolts (a.k.a. Dry Torque)
- Partially Lubricated Bolts
- Properly Lubricated Bolts
But before we talk about these items, or get to our torque chart, it is imperative you understand the working definition of K-Factor (or “Nut Factor”). ASME PCC-1 states:
“K is an experimentally determined, dimensionless constant related to the coefficient of friction.”
Translation: You need to have experimental data on what Nut Factor you have. DO NOT rely on just the coefficient of friction numbers. Some manufacturers will say they are the same, or they will not have done Nut Factor testing at all. PLEASE do your homework on this.
“Published tables of experimental nut factors are available from a number of sources; however, care must be taken to ensure that the factors are applicable to the application being considered.”
Translation: You need to make sure any previous testing was done on applications that represent what you are working with. For example, we once saw a company do a test on 1/4 inch bolts. The problem: The average size bolt in the petrochemcial industry is 3/4 inch. So those tests weren’t especially helpful.
“It should also be noted that recent research has shown there to be nut factor dependence on bolt material, bolt diameter, and assembly temperature. These factors can be significant and should not be ignored when selecting the nut factor or anti-seize compound. The user is advised either to seek test results conducted on similar bolt and anti-seize specifications or to conduct nut factortrials (size and material) with their own conditions.”
Translation: Get your hands on their research! It’s the only way you can verify that they have done their homework.
(Beyond ASME PCC-1: Learn what today’s bolting professionals need to know.)
Non-Lubricated Bolt Nut Factor:
It’s not possible to determine an accurate Nut Factor for dry threads. Unfortunately, when you don’t have lubricant, there are many other substances that may act as lubes on your fastener that you might not be able to see.
One of them is the oil used on them during manufacturing. For example, we have seen a stud where the oil has been “baked off” using an oven have a Nut Factor of about .26, while a stud that still has oil residue is about a .20. (It’s worth noting that particles of solids still on the stud that will also affect your Nut Factor).
That is a big discrepancy.
Hex Technology recommends that you do not try to solve this problem unless you have the proper equipment and understand the “Turn of the Nut Method.”
Partially Lubricated Bolt Nut Factor:
Let’s say you’ve done your homework and understand the nut factor for your lube. If that lubricant isn’t applied generously/properly, the dry parts of the fastener will increase your Nut Factor and result in different bolt loads on each of your fasteners.
So you might be using a calibrated torque wrench, and have a known Nut Factor, but if your lube isn’t applied properly, your torque value (bolt tension) will have changed.
(Learn more about how to properly use clicker wrenches.)
Properly Lubricated Bolt Nut Factor:
When testing your Nut Factor, you put it in the best and most repeatable condition, then you replicate those conditions in the field. By properly lubricating fasteners, you achieve the correct ft-lbs, clamping force/preload, and gasket stress.
How Much Lubricant Should You Use?
Proper lubrication means that you’ve put lubricant on every thread so that the valley of the stud is full.
Notice how we lubricate enough so that when you hand rotate the nut down, there’s a little bead of lube that squishes out. This means that we’ve put lubricant on all the parts that will experience friction when we apply torque.
How to Apply Bolt Lubricant
When you apply lubricant, be certain that all valleys of the stud bolt threads are filled.
Once the nut is hand tightened, you should see a bead of lubricant extruding from beneath the nut. This indicates that the lubrication has been applied to all working surfaces.
In this screenshot from the video above, notice how the varying levels of bolt lubrication lead to better results:

No lubrication: You will see that, without lubricant, bolt stress is lower than our target bolt stress of 40 Ksi. In the video above, our test on unlubricated studs test averages 28.8 Ksi, with the low amount being 27.3 and a high of 31.
Partial lubrication: Inconsistent or only partially lubricating the studs will result in unfavorable bolt stress. In the second test, by using lubricant the average bolt stress increased by 5.4 Ksi, but still came up short of our target of 40 Ksi. Bolts that are not lubricated in the same fashion will have a greater variation in the bolt load.
Proper lubrication: Properly lubricated studs will result in a tight bolt load at our desired stress target. Notice how bolt load has increased, and we’re now achieving bolt loads much closer to the target bolt load of 40 Ksi. And notice how the variation among the bolt loads (a.k.a. bolt scatter) has drastically reduced when all working surfaces are properly lubricated.
Bolt Lubricant Torque Chart
PCC-1 published Table O-3.2-1 “Reference Values (Target Torque Index) for Calculating Target Torque Values for Low-Alloy Bolting Based on Unit Prestress of 1 ksi (root area) (Inch Series Threads).
This was done to ensure you can use it to determine and adjust to stainless steel fasteners that have a lower tensile strength.
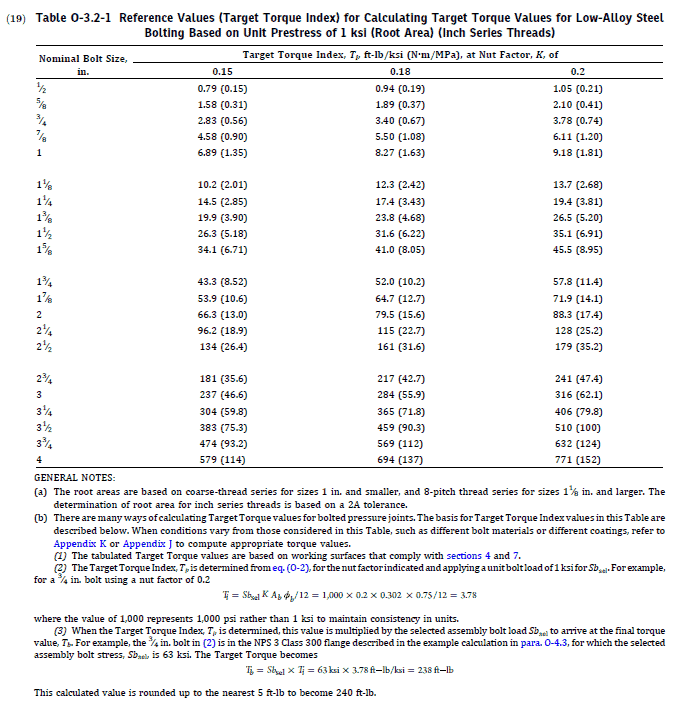
NOTE: The above chart shows you how to determine your torque IF you have either a 0.15, 0.18, OR 0.2 Nut Factor. But again you need to experiment with what lube you have and confirm the Nut Factor is in order to make a torque specification.
Related Articles:
How to Prevent Galling (and “Fake” Galling)
Learn more about the technical aspects of bolted flange joint assembly.
Join Industry Leaders!
Subscribe to Hex Technology today and we’ll give you $700 in bolting courses, FREE. Your path to a safer, more reliable, more profitable site starts here.